Mechanical Performance and Metallurgical Features of ProTaper Universal and 6 Replicalike Systems
Abstract
Introduction: This study aimed to compare the ProTaper Universal (PTU; Dentsply Maillefer, Ballaigues, Switzerland) system with 6 replicalike instruments regarding instrument design, mechanical performance, and alloy characteristics.
Methods: New rotary instruments (size 20/.07v) of PTU and 6 replicalike systems (EdgeTaper [EdgeEndo, Johnson City, TN], U-File [Dentmark, Ludhiana, India], Go-Taper Universal [Access, Shenzhen, China], Super Files [Flydent, Shenzhen, China], Multitaper [Proclinic Expert, Besançon, France], and Pluri Taper [Bestdent, Shenzhen, China]) (n = 329) were selected and evaluated regarding their design, mechanical performance, and metallurgical characteristics. The results were compared using the nonparametric Mood median test and 1-way analysis of variance with the significance level set at 0.05.
Results: Replicalike instruments were similar to PTU regarding design, maximum torque to fracture (P ˃ .05), and ratio of nickel and titanium elements. Scanning electron microscopy revealed differences in the geometry of the tip and finishing surfaces. Time to fracture of Go-Taper Universal (50.0 seconds) was similar to PTU (44.0 seconds) (P ˃ .05), but the U-File (63.5 seconds), Edge Taper (87.5 seconds), and Super Files (130 seconds) showed significantly higher values (P ˂ .05). The highest maximum torque was observed in the Super Files instrument (P ˂ .05), but no statistical difference was noted among the other instruments (P ˃ .05). The angle of rotation before rupture of the Multitaper (574°) and Pluri Taper (481°) was higher than PTU (354°) (P ˂ .05). Differential scanning calorimetric analysis showed clear differences on the transformation temperatures among the tested instruments. The R-phase start and finish temperatures of PTU were 11.0°C and 218.0°C, respectively.
Conclusions: Overall, replicalike instruments were similar to PTU regarding the torsional resistance, geometric design, and near equiatomic proportions of nickel and titanium elements. In 3 of the 4 mechanical tests, the EdgeTaper (torque, angle of rotation, and bending load) and Go-Taper Universal (time to fracture, torque, and angle of rotation) systems were similar to PTU. (J Endod 2020;■:1–10.)
Over the last decade, several nickel-titanium (NiTi) rotary systems have been proposed by dental companies for the mechanical preparation of the root canal system. The manufacture of these instruments should follow a standard flow of internal research, development, production testing, and marketing with controlled standards of quality. However, currently, several companies worldwide started to produce and/or distribute NiTi instruments with similar characteristics to well-known brand systems without clear reports on production control quality or international certification. These instruments, although they are different brands, present similar characteristics to the original ones, such as the number/sequence of instruments, nomenclature, and identification (color coding); they are named replicalike systems. Replicalike systems have been commercialized worldwide by local distributers and are accessible via the Internet at lower prices, which may be appealing for several professionals, as recently reported by Logsdon et al. On the other hand, the clinical safety and efficiency of most of these systems were not confirmed yet from a scientific perspective, or the data are scarce compared with the original brand counterparts.
ProTaper Universal (PTU; Dentsply Maillefer, Ballaigues, Switzerland) is 1 of the most well-known and long-lasting available rotary systems made of conventional NiTi alloy on the market currently. At the time it was launched, its innovative progressive tapered design was regarded to contribute to PTU becoming 1 of the best selling systems in the world; therefore, it has been used for root canal preparation in several countries.
Accordingly, throughout the years, replicalike systems of PTU have been manufactured by different companies including EdgeTaper (EdgeEndo, Johnson City, TN), U-File (Dentmark, Ludhiana, India), Go-Taper Universal (Access, Shenzhen, China), Super Files (Flydent, Shenzhen, China), Multitaper (Proclinic Expert, Besançon, France), and Pluri Taper (Bestdent, Shenzhen, China), among others. So far, despite these replicalike instruments being commercially available locally in American, European, and Asian continents and worldwide through online shops, there is a lack of information on their quality, performance, and safety for clinical use in the literature in comparison with the original brand systems. Therefore, this article set out to run a comprehensive laboratorial assessment of 6 replicalike instruments of the original PTU brand system regarding design, mechanical performance, and alloy characteristics. The null hypothesis to be tested was that there were no differences between the original and replicalike instruments regarding their mechanical efficiency and metal alloy features.
Materials and Methods
A total of 329 new 25-mm NiTi rotary size 20/.07v instruments collected from a premium brand (PTU system) and 6 replicalike systems (n = 47 per group) (Table 1, Fig. 1) were evaluated regarding their design, mechanical performance, and metallurgical characteristics.
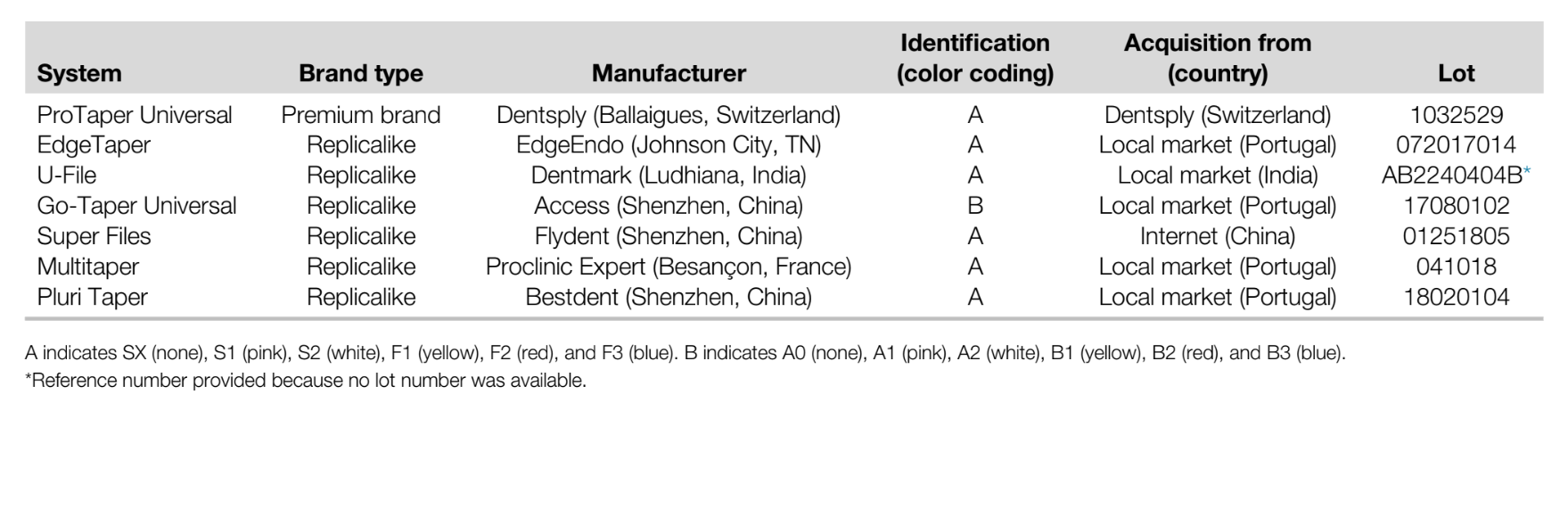
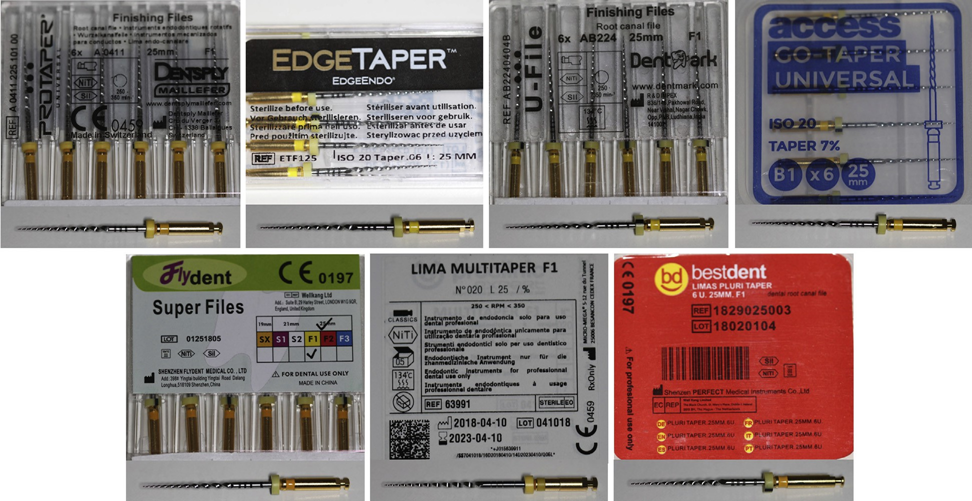
Instrument Design
Six instruments from each system were randomly selected and submitted to stereomicroscopic visual inspection under x3.4 and x13.6 magnifications using a dental operating microscope (Opmi Pico; Carl Zeiss, Jena, Germany) equipped with a Canon EOS 500D camera (Canon, Tokyo, Japan) in order to record the following characteristics:
- The number of active blades (in units)
- The helix angle of the active blade based on the average measurements of the 6 most coronal angles assessed in triplicate
- The distance (in mm) from the instruments’ tips to the 3 measuring lines (18, 20, and 22 mm) at their noncutting part measured by a digital caliper with a resolution of 0.01 mm (Mitutoyo, Aurora, IL). Discrepancies were considered significant when values were higher than 0.1 mm from the reference line. This process was repeated 3 times, and the mean reading was recorded.
- The identification of major defects or deformations (ie, file distortion and missing or twisted blades)
Then, the same instruments were prepared for conventional scanning electron microscopic analysis (S-2400; Hitachi, Tokyo, Japan) and evaluated regarding the following:
- the spiral design at the middle portion of the active part (symmetrical or asymmetrical),
- the tip (active or nonactive),
- the cross-sectional design,
- the presence of surface marks (machined production process), and
- minor manufacturer defects or deformations.
Mechanical Tests
Cyclic fatigue, torsional, and bending resistance tests were used to evaluate the mechanical performance of the selected systems. First, sample size calculation with 80% power and an alpha of 0.05 was performed for each test based on the highest difference obtained in the 6 initial measurements between the original brand (PTU) and 1 of the replicalike systems. For time to fracture (PTU vs Super Files), a final sample size of 7 instruments was determined based on an effect size of 94.67 (657.52). For the maximum torque and angle of rotation in the torsional test (PTU vs Multitaper), sample sizes of 12 and 7 instruments were established considering effect sizes of 0.30 (60.24) and 214.16 (6122.87), respectively, whereas for the maximum load in the bending test (PTU vs Multitaper), an effect size of 74.16 (639.69) resulted in a final sample size of 6 instruments. Therefore, a total of 12 instruments per group was defined for each dependent variable. However, before the tests, all instruments were submitted to a stereomicroscopic visual inspection (x13.6) to detect defects or deformations that would be exclusion criteria. No deformed instruments were found. All tests were performed at room temperature (20°C).
The cyclic fatigue resistance test was performed on a severely curved artificial canal using previously tested static model conditions and followed the rotation motion recommended by the manufacturers.
Instruments were mounted on a 6:1 reduction handpiece (VDW/Sirona Dental Systems, Bensheim, Germany) powered by an electric motor (Reciproc Silver; VDW GmbH, Munich, Germany) and assembled on a tube model custom-made device. The artificial canal was created on a stainless steel tube. The tube was 19-mm long and was composed of 3 segments. The first segment was a 7-mm straight coronal segment. The second was a 9-mm-long curve with a 6-mm radius and 86° of curvature, with the position of maximum stress in the middle of the curvature length. The third was a 3-mm straight apical segment. The instruments rotated freely inside the canal using glycerin as the lubricant. The fracture moment was noted both visually and audibly. Time to fracture (in seconds) was recorded using a digital chronometer, and the fragment size of the instruments (in millimeters) was measured with a digital caliper (Mitutoyo, Aurora, IL). No camera recording was used. The torsional resistance test was performed in a static torsion model following the ISO 3630 and 3631 specifications. Instruments were mounted in a straight position on a torsiometer TT100 (Odeme Dental Research, Luzerna, Santa Catarina, Brazil) clamped at their apical 3 mm and rotated on a constant 2-rpm pace in the clockwise direction until fracture. The maximum torque sustained before rupture (in Ncm) and the angle of rotation (in °) were recorded. The bending resistance test was conducted according to the ISO 3630 and 3631 specifications. Instruments were mounted pointing down in a 45° position regarding the floor plane by their grip in the file holder of the motor while having their apical 3 mm attached to a wire linked to a universal testing machine (Instron EMIC DL- 200 MF, São Josédos Pinhais, Brazil). The test was performed by applying a load of 20 N at a 15-mm/min constant pace until the instrument underwent a displacement of 45°. The maximum load required to induce the 45° displacement was recorded in gram-force (gf) (Fig. 2).
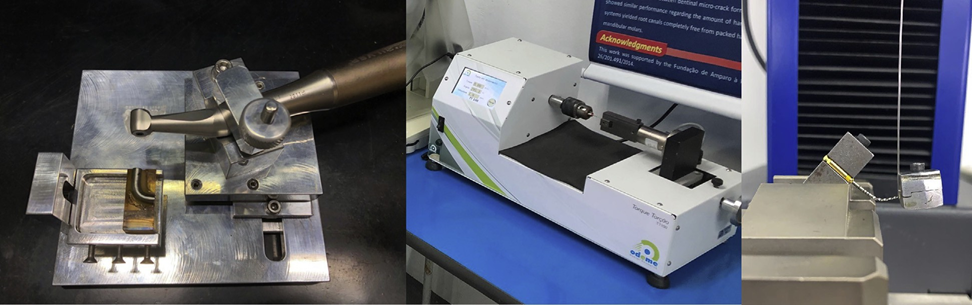
Metallurgical Characterization Metallurgical characterization of the instruments was depicted using energy-dispersive X-ray spectroscopy (EDS) and differential scanning calorimetry (DSC). Three instruments from each system were analyzed on a conventional scanning electron microscope (Carl Zeiss) and the Inca X-act EDS detector (Oxford Instruments NanoAnalysis, Abingdon, UK).
Acquisitions were made with a 60-second lifetime for optimized image conditions with an approximately 30% death time, covering an instrument area of 500 x 400 mm. The elemental EDS analysis was semiquantitative using the ZAF correction (Microanalysis Suite v.4.14 software, Oxford Instruments NanoAnalysis) from which the proportions of nickel and titanium were extracted. For the DSC analysis (DSC 204 F1 Phoenix; Netzsch-Gerätebau GmbH, Selb, Germany), which followed the guidelines from the American Society for Testing and Materials, a 3- to 5-mm fragment of each instrument was removed from its coronal active blade, exposed to a chemical etching bath (25% hydrofluoric acid, 45% nitric acid, and 30% distilled water) for approximately 2 minutes, and submitted to individual thermal cycles. The thermal cycle started with room temperature stabilization for 2 minutes and then was heated up to 150°C with a pace of 10°C/min. At the maximum temperature level, a stabilization plateau was performed for 2 minutes, and then a cooling cycle was started, which decreased until 2150°C at a pace of 10°C/min, followed by another 2-minute stabilization plateau. Then, a new heating phase was induced until 150°C at a pace of 10°C followed by a 2-minute stabilization plateau. Finally, the temperature decreased to room temperature, and 1 last 2-minute stabilization plateau was performed. The results were analyzed using the Netzsch Proteus Thermal Analysis software (Netzsch-Gerätebau GmbH). Two tests (A and B) on 2 different fragments removed from the same position from 2 different instruments of each group were conducted. The second test (B) intended to confirm the results of the first one (A).
Statistical Analysis
The results of the dependent variables helix angle, time to fracture, maximum torque, angle of rotation, and maximum load showed non-Gaussian distribution (Shapiro-Wilk test, P ˂ .05) and were compared using the nonparametric Mood median test, whereas fragment length was evaluated by 1-way analysis of variance (Shapiro-Wilk test, P ˃ .05). The significance level was set at 0.05 (SPSS v.22 software; IBM Corp, Armonk, NY).
Results
Instrument Design
Overall, replicalike instruments were similar to the premium brand (PTU) regarding the number of blades and the helix angle (P ˃ .05), whereas no major defects or deformations were observed. The optimal matched positions of the measuring lines were observed in the PTU, Multitaper, and Pluri Taper brands, whereas the other instruments showed discrepancies higher than 0.1 mm (Table 2). The position of the measuring lines was more consistent in the original PTU, whereas most of the replicalike instruments showeddiscrepancy results (Table 2). Scanning electron microscopic analysis (Fig. 3) confirmed the design similarities among instruments with symmetrical spiral designs without radial lands, although the Multitaper cross-sectional shape was more triangular than the convex triangular shape of the other instruments. The geometry of the tip in all replicalike instruments was different from the ProTaper system, with the closest design being observed in the MultiTaper instrument. None of the tested instruments displayed an active tip, but the distance from the tip to the transition angle of the blade varied from instrument to instrument (Fig. 3). At higher magnification, it was possible to observe differences in their finishing surfaces. Super Files showed less irregularities and manufacturing marks, whereas the worst finishing surface was observed in the Multitaper and Pluri Taper instruments (Fig. 4).
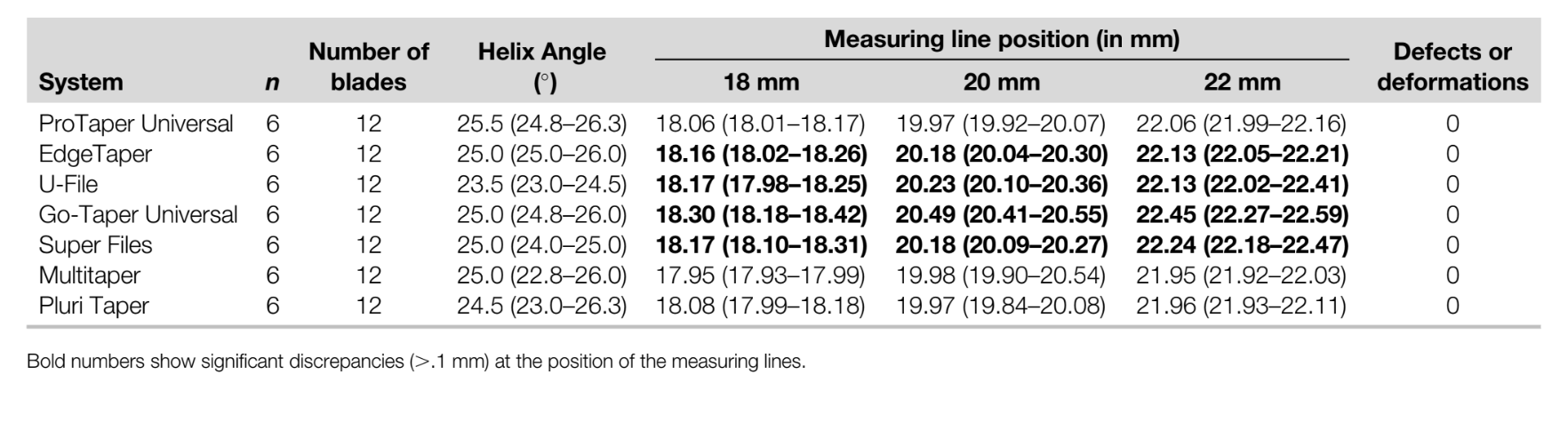
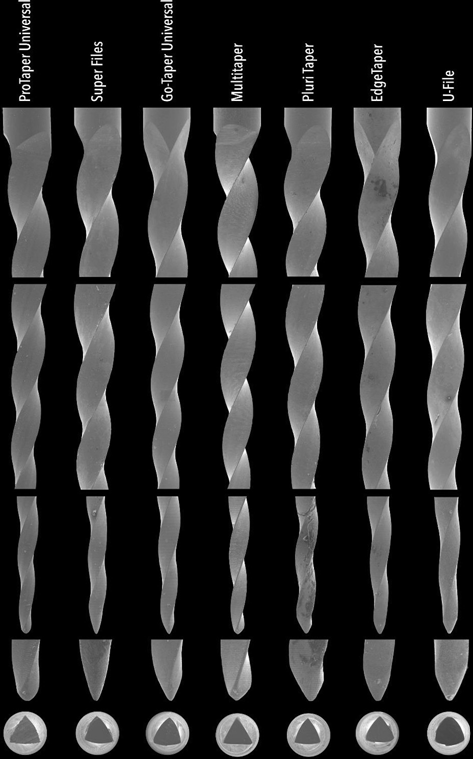
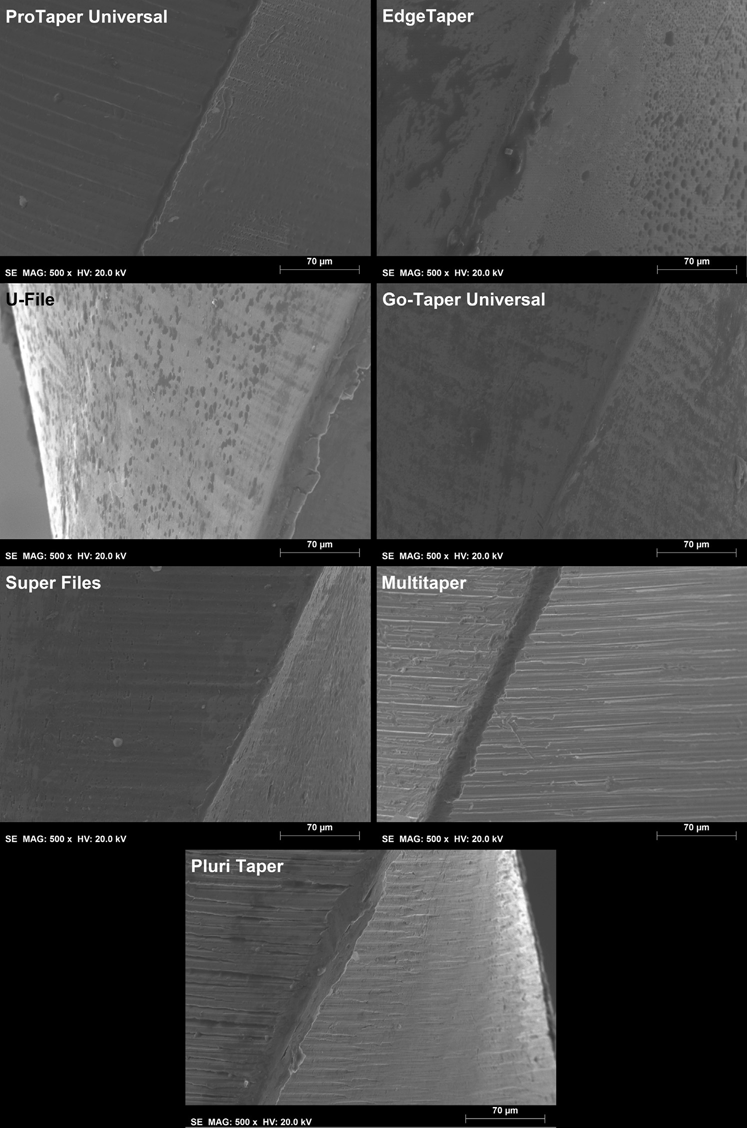
Mechanical Tests
Table 3 and Figure 5 summarize the results from the mechanical tests. In the cyclic fatigue test, no difference was observed regarding the length of the fragments (P ˃ .05), demonstrating the correct position of the instruments within the artificial canal during the test. Time to fracture of Go-Taper Universal (50.0 seconds) was similar to the PTU (44.0 seconds) (P ˃ .05), but U-File (63.5 seconds), Edge Taper (87.5 seconds), and Super Files (130 seconds) showed significantly higher values than the premium brand system (P ˂ .05). The highest median maximum torque was observed in the Super Files instrument (1.45 Ncm), but no statistical difference was noted among the tested instruments (P ˃ .05). The median angle of rotation before the rupture of the Multitaper (574°) and Pluri Taper (481°) instruments was higher than PTU (354°) (P ˂ .05), whereas no difference was observed among the other systems (P ˃ .05). On the bending test, only EdgeTaper (411.0 gf) showed no significant difference compared with PTU (395.1 gf) (P ˃ .05). The Go-Taper Universal (456.3 gf) and U-File (466.5 gf) instruments showed higher values than PTU (P ˂ .05), whereas lower results were obtained with the Pluri Taper (344.4 gf), Super Files (347.6 gf), and Multitaper (321.4 gf) instruments.
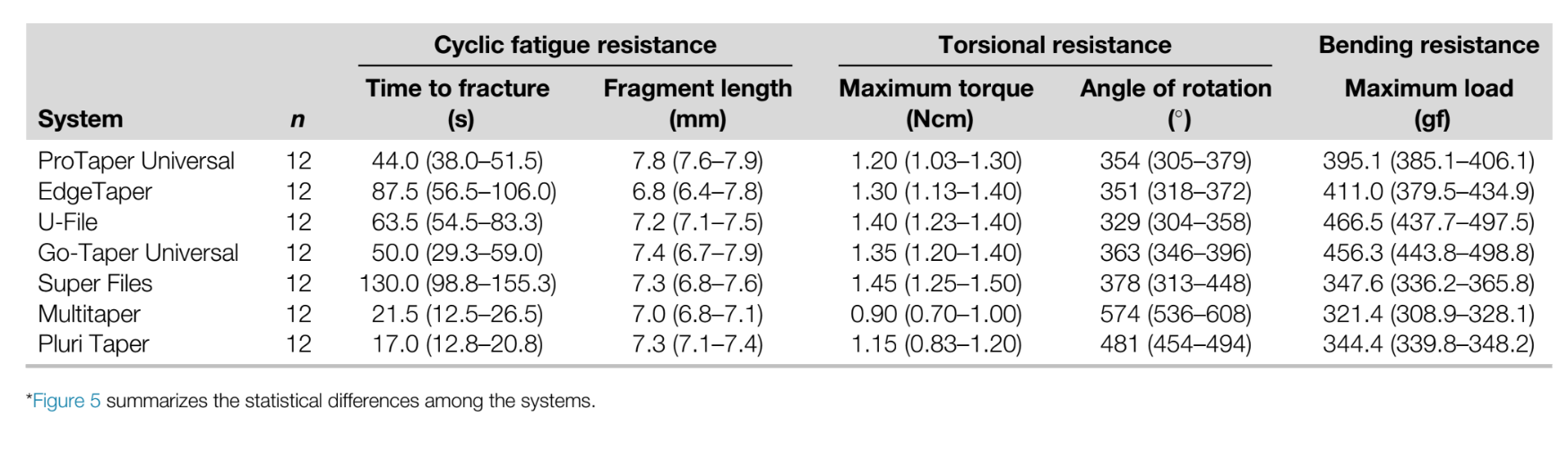
Metallurgical Characterization
EDS assessment revealed that all instruments had an almost equiatomic ratio between the nickel and titanium elements. DSC analysis showed differences on the phase transformation temperatures among instruments, with some of them presenting martensitic characteristics and others full austenitic characteristics at the testing temperature (20°C). For the original PTU instrument, the R-phase start (Rs) and finish (Rf) temperatures were 11.0°C and 218.0°C, respectively, whereas the Multitaper showed the flattest R-phase (Rs: 18.1°C and Rf: 245.2°C) and Super Files the highest Rs among the instruments (37.7°C) and the closest Rf (14.1°C) to the testing temperature. The Rs temperatures of 3 replicalike systems (Pluri Taper [17.9°C], Multitaper [18.1°C], and Edge Taper [18.8°C]) were lower than the testing temperature, whereas the other 3 were higher (Super Files [37.7°C], Go-Taper Universal [27.8°C], and U-File [21.4°C]) (Fig. 6).
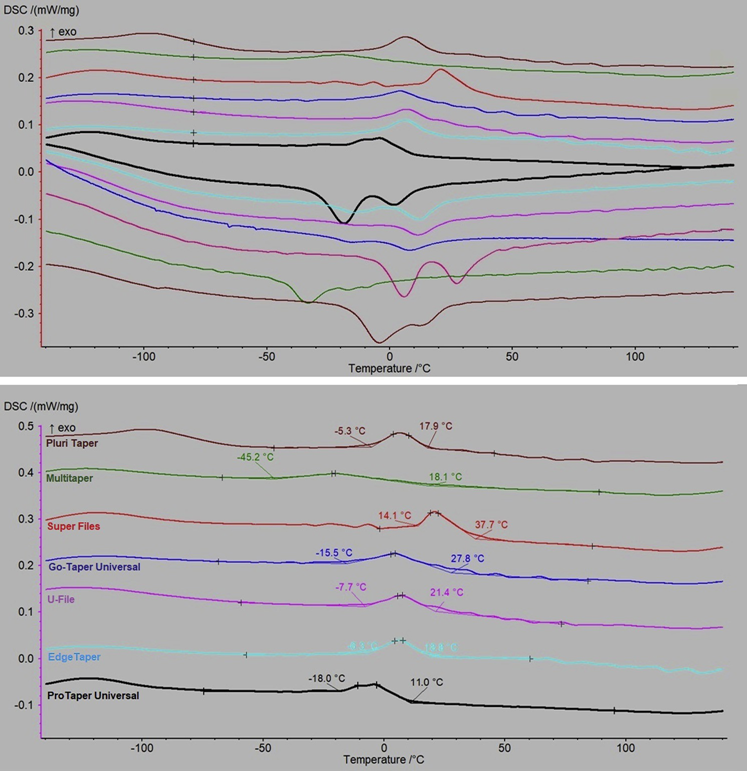
Discussion
Over the last years, a new phenomenon has been observed in the dental market with corporations of major emerging economic countries, such as China and India, manufacturing and marketing dental goods worldwide, including engine-driven endodontic systems. Although some of these companies have developed innovative instruments for the mechanical preparation of root canals, others just copy or imitate the physical appearance of well-known products, the so-called replicalike systems. Nonetheless, the lack of international regulatory tools does not allow for imposing standards for quality control to guide the production of rotary/reciprocating NiTi systems, and clinicians are often unaware of the risks involved in using products with no scientific background regarding their safety.
Accordingly, this study is the first to provide new insights into the mechanical performance of 6 commercially available replicalike instruments of the original PTU brand (Fig. 1). Cyclic fatigue resistance, maximum torque, angle of rotation, and bending load behavior of the original PTU system were used as a control for the evaluation of replicalike systems, and, considering the significant differences in the tested dependent variables, the null hypothesis was rejected. However, it is important to highlight that these parameters were interconnected with several other variables including their manufacturing quality, metallurgical properties, and geometric shapes. Therefore, the multimethod analytical approach used in this study would be the most appropriate procedure for a comprehensive understanding of the mechanical behavior of these engine-driven NiTi instruments.
Overall, scanning electron microscopic/ EDS analysis showed that replicalike instruments were similar to the PTU regarding the geometric design (Fig. 3) and the near equiatomic proportions of nickel and titanium elements, which partially explain their similarities in the torsional resistance test (Fig. 5). Hence, it may be inferred that differences in the other dependent tested variables were mostly related to the quality of the manufacturing process as well as the dissimilarities in their martensitic-austenitic transformation phases at specific temperatures (Fig. 6). For instance, the Rs temperatures of 3 replicalike systems (Pluri Taper, Multitaper, and Edge Taper) were lower than the testing temperature (20°C), giving them a total austenitic phase constitution, whereas the other 3 (Super Files, Go-Taper Universal, and U-File) were higher, indicating that some martensitic characteristics were still present. Therefore, these differences will partially explain most of the observed results.
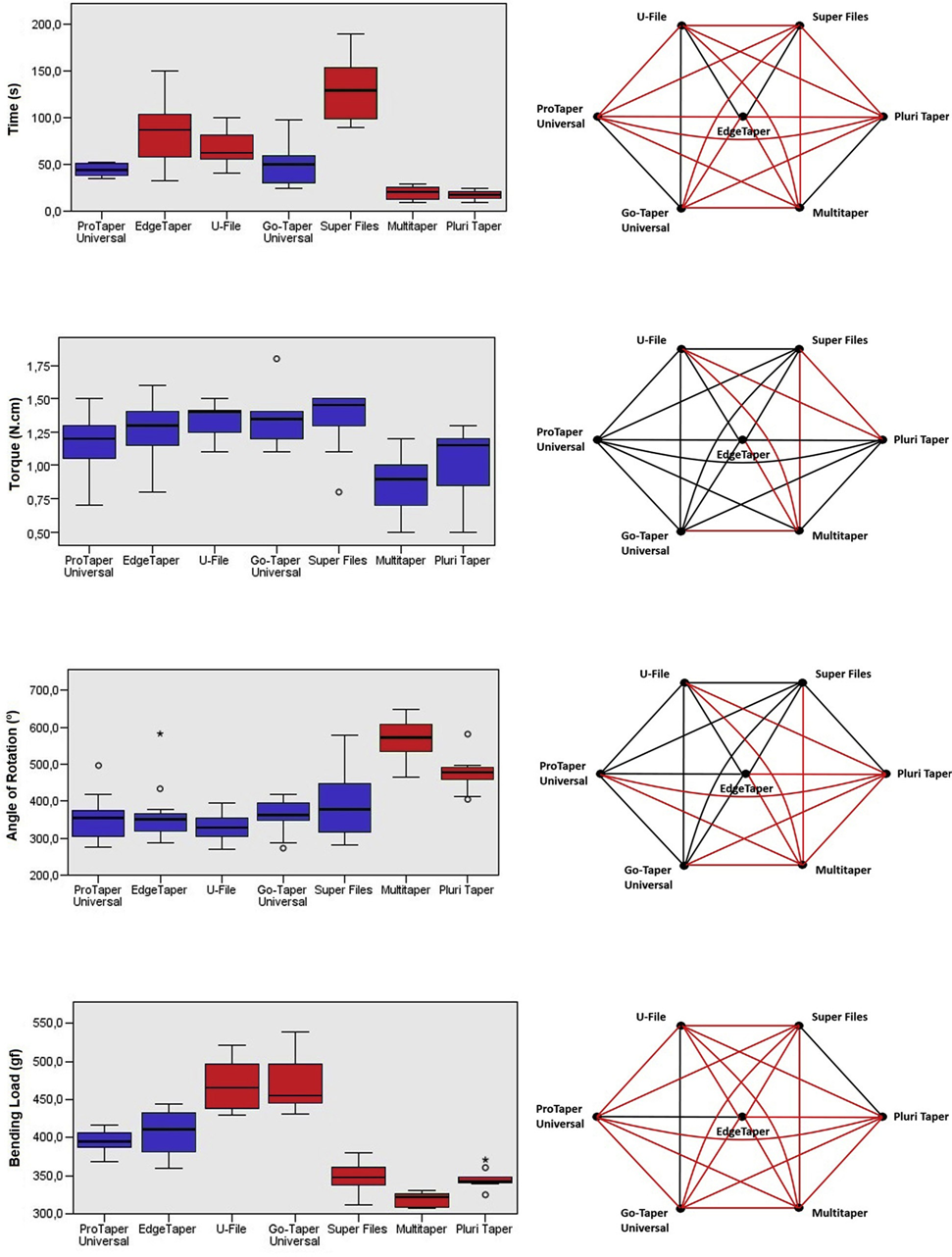
In clinics, cyclic flexural fatigue of an instrument occurs when it rotates in a curved canal by repeated cycles of compressive and tensile stresses, whereas torsional failure is caused by local embedment of dentinal chips in machining grooves or inadvertent wedging of the tip of the instrument in the root canal wall. Both cyclic fatigue and torsional resistance parameters represent mechanical resistance measures whose improvements anticipate better clinical performance when submitted to that specific stress reducing the chance of instrument fracture. The angle of rotation value represents the capacity to sustain deformation before fracture under torsional stress, whereas the maximum bending load value (less bending load required means higher flexibility) represents a flexibility measure. Flexibility is accepted as a characteristic that may be able to improve root canal shaping by minimizing the possibility of deviation from the original root canal pathway. In the cyclic fatigue test, the Multitaper and Pluri Taper showed the lowest time to fracture among all instruments (Fig. 5), and this may be related to their poorer surface finishing, as observed in the scanning electron microscopic analysis (Figs. 3 and 4). Surprisingly, despite their similar austenitic nature to PTU (Fig. 6), higher angles of rotation before rupture were observed, corroborating the low stiffness demonstrated in the bending test (Fig. 5). Despite these findings appearing contradictory, it is possible that another aspect related to their designs, such as the core diameter, tip size, taper, and percentage of contaminants added to the alloy during the manufacturing process, which were not assessed in this study, had influenced the results. On the other hand, time to fracture of Super Files and U-File was significantly higher than PTU (Table 3, Fig. 5), possibly because of the predominant martensitic characteristics (Fig. 6), which have been considered an important factor to increase the cyclic fatigue resistance. Interestingly, despite the fact that the NiTi alloy of the Go-Taper Universal system is also partially martensitic (Fig. 6), it showed low flexibility compared with PTU and no difference in cyclic fatigue resistance (Fig. 5). As previously discussed, it is possible that another aspect related to its design and not assessed in the current study has influenced the results. Finally, time to fracture of EdgeTaper was higher than PTU, despite similarities in terms of flexibility (Fig. 5) and their austenite nature (Fig. 6). However, it may be noticed that the peak of EdgeTaper to the initial transformation of martensitic is completed at 18.8°C, which means that it is at the edge of the testing temperature (20◦C). Consequently, it is possible that its attrition with the stainless steel surface of the artificial canal during the cyclic fatigue test has raised the temperature and changed the instrument phase, which explains the present findings.
Notwithstanding variations reported in the literature, torsional load to separation and bending resistance tests have been accepted as reliable methodologies for testing the mechanical behavior of endodontic instruments because their requirements are well described in international guidelines. In contrast, cyclic fatigue tests have been the subject of an extensive debate over the years. Basically, in the fatigue test using a static model, the instrument is mounted in a stabilized handpiece and made to rotate freely in an artificial canal until its fracture. Obviously, as in most bench research and considering the multivariable nature of instrument failure, translating these results to clinics may not be appropriated. On the other hand, under the same conditions, the cyclic fatigue test allows avoidance of interference of different variables by isolating and testing factors individually, increasing the internal validity of the method. One of these variables is the motion type in which the dynamic mode has been proposed as an alternative to the static one. However, this method has been described as presenting lower internal validity compared with the static method because it might not be possible to consistently maintain the tested instruments in a reproducible trajectory throughout the simulated canal path. Another variable is the testing temperature. A recent review suggested that testing cyclic fatigue at room temperature should be regarded as having little meaning and outdated, whereas others advocated the use of body/intracanal temperature. It is important to pointout that most instruments submitted to cyclic fatigue tests under body temperature suffer a decrease of their fatigue resistance as a result of the increased temperature transmitted from the warmed artificial canal to the metal alloy of the instrument, which, depending on the phase transformation temperature range, may induce partial or total austenitic formation.
However, in clinics, it is unlikely that the short time in which the instrument contacts the root canal walls would rise and stabilize the temperature at a point to induce phase changes that may further interfere with the outcome. Besides, the irrigant solution, normally used under room temperature, and the thermal insulating efficiency of the dentin are also factors that may prevent the instrument to reach body temperature.
Therefore, the assumption that the cyclic fatigue test must be conducted under body temperature to mimic a clinical setup still lacks validation; room temperature was chosen in this study to perform the tests because this is the temperature in which the instruments are usually stored and used in practice.
In this study, the mechanical behavior of the selected instruments was compared regarding cyclic fatigue, torsional, and bending properties, and a comprehensive understanding of the results was possible only because of the further evaluation of their overall designs, finishing surfaces, and metallurgical characteristics. It is important to underline that the present results are original because no information is available in the literature or from the manufacturers regarding the replicalike instruments; thus, our results bring some light on their mechanical behavior. The novelty regarding the multimethod analytical approach and the evaluation of replicalike instruments can be considered strengths of the present study, whereas other design factors that were not assessed and the evaluation of only 1 instrument (20/.07v) from each system are limitations. Therefore, further studies should focus not only on the evaluation of other replicalike instruments available in the market but also on counterfeit systems, while trying to evaluate other design aspects as well, including additional methodologies for testing shaping ability and cutting efficiency.
Conclusions
Overall, replicalike instruments were similar to PTU regarding the torsional resistance, the geometric design, and the equiatomic proportions of nickel and titanium elements. EdgeTaper and Go-Taper Universal were similar to PTU in 3 of the 4 mechanical tests. The Multitaper and Pluri Taper instruments had more flexibility but lower time to fracture than PTU. Super Files, EdgeTaper, and U-File showed the highest cyclic fatigue resistance among the tested instruments.
Authors: Jorge N. R. Martins, Emmanuel J. N. L. Silva, Duarte Marques, Mário Rito Pereira, António Ginjeira, Rui J. C. Silva, Francisco Manuel Braz Fernandes, Marco Aurélio Versiani
References:
- Gavini G, Santos MD, Caldeira CL, et al. Nickel-titanium instruments in endodontics: a concise review of the state of the art. Braz Oral Res 2018;32:e67.
- Tabassum S, Zafar K, Umer F. Nickel-titanium rotary file systems: what’s new? Eur Endod J 2019;4:111–7.
- Martins JN, Nogueira Leal Silva EJ, Marques D, et al. Influence of kinematics on the cyclic fatigue resistance of replicalike and original brand rotary instruments. J Endod 2020;46:1136–43.
- Logsdon J, Dunlap C, Arias A, et al. Current trends in use and reuse of nickel-titanium engine- driven instruments: a survey of endodontists in the United States. J Endod 2020;46:391–6.
- De-Deus G, Marins J, Silva EJ, et al. Accumulated hard tissue debris produced during reciprocating and rotary nickel-titanium canal preparation. J Endod 2015;41:676–81.
- Elnaghy AM, Elsaka SE. Mechanical properties of ProTaper Gold nickel-titanium rotary instruments. Int Endod J 2016;49:1073–8.
- Hieawy A, Haapasalo M, Zhou H, et al. Phase transformation behavior and resistance to bending and cyclic fatigue of ProTaper Gold and ProTaper Universal instruments. J Endod 2015;41:1134–8.
- Plotino G, Grande NM, Mercade Bellido M, et al. Influence of temperature on cyclic fatigue resistance of ProTaper Gold and ProTaper Universal rotary files. J Endod 2017;43:200–2.
- Ruddle CJ, Machtou P, West JD. The shaping movement: fifth-generation technology. Dent Today 2013;32:96–9.
- Locke M, Thomas MB, Dummer PM. A survey of adoption of endodontic nickel-titanium rotary instrumentation part 1: general dental practitioners in Wales. Br Dent J 2013;214:E6.
- Patil TN, Saraf PA, Penukonda R, et al. A survey on nickel titanium rotary instruments and their usage techniques by endodontists in India. J Clin Diagn Res 2017;11:ZC29–35.
- Sydney GB, Santos IM, Batista A, et al. A implementaça~o do uso dos sistemas rotato´rio em endodontia. Rev Odontol Bras Central 2014;23:113–20.
- ANSI/ADA Specification no. 28. Root canal files and reamers, type K for hand use. Chicago, IL: American Dental Association; 2002.
- ISO3630-3631:2008. Dentistry – root canal instruments – part 1: general requirements and test methods.
- ASTM F2004 2 17: standard test method for transformation temperature of nickel-titanium alloys by thermal analysis. West Conshohocken, PA: ASTM International; 2017. Available at: www.astm.org. Accessed September 29, 2020.
- Silva E, Vieira VT, Hecksher F, et al. Cyclic fatigue using severely curved canals and torsional resistance of thermally treated reciprocating instruments. Clin Oral Investig 2018;22:2633–8.
- Anderson ME, Price JW, Parashos P. Fracture resistance of electropolished rotary nickel- titanium endodontic instruments. J Endod 2007;33:1212–6.
- de Vasconcelos RA, Murphy S, Carvalho CA, et al. Evidence for reduced fatigue resistance of contemporary rotary instruments exposed to body temperature. J Endod 2016;42:782–7.
- De-Deus G, Silva EJ, Vieira VT, et al. Blue thermomechanical treatment optimizes fatigue resistance and flexibility of the reciproc files. J Endod 2017;43:462–6.
- Goo HJ, Kwak SW, Ha JH, et al. Mechanical properties of various heat-treated nickel-titanium rotary instruments. J Endod 2017;43:1872–7.
- Zhou H, Peng B, Zheng Y. An overview of the mechanical properties of nickel–titanium endodontic instruments. Endod Topics 2013;29:42–54.
- Alcalde MP, Tanomaru-Filho M, Bramante CM, et al. Cyclic and torsional fatigue resistance of reciprocating single files manufactured by different nickel-titanium alloys. J Endod 2017;43:1186–91.
- Ebihara A, Yahata Y, Miyara K, et al. Heat treatment of nickel-titanium rotary endodontic instruments: effects on bending properties and shaping abilities. Int Endod J 2011;44:843–9.
- Galvao Barbosa FO, Ponciano Gomes JA, Pimenta de Araujo MC. Influence of previous angular deformation on flexural fatigue resistance of K3 nickel-titanium rotary instruments. J Endod 2007;33:1477–80.
- Hulsmann M, Donnermeyer D, Schafer E. A critical appraisal of studies on cyclic fatigue resistance of engine-driven endodontic instruments. Int Endod J 2019;52:1427–45.
- Peters OA, Arias A, Choi A. Mechanical properties of a novel nickel-titanium root canal instrument: stationary and dynamic tests. J Endod 2020;46:994–1001.
- Plotino G, Grande NM, Cordaro M, et al. A review of cyclic fatigue testing of nickel-titanium rotary instruments. J Endod 2009;35:1469–76.
- Huang X, Shen Y, Wei X, Haapasalo M. Fatigue resistance of nickel-titanium instruments exposed to high-concentration hypochlorite. J Endod 2017;43:1847–51.
- Keles A, Eymirli A, Uyanik O, Nagas E. Influence of static and dynamic cyclic fatigue tests on the lifespan of four reciprocating systems at different temperatures. Int Endod J 2019;52:880–6.
- Thompson SA. An overview of nickel-titanium alloys used in dentistry. Int Endod J 2000;33: 297–310.