Evaluation of Design, Metallurgy, Microhardness, and Mechanical Properties of Glide Path Instruments: A Multimethod Approach
Abstract
Introduction: This study aims to compare the design, metallurgy, microhardness, and mechanical properties of 3 glide path nickel-titanium (NiTi) instruments.
Methods: A total of 132 ProGlider (Dentsply Sirona, Ballaigues, Switzerland), Edge Glide Path (EdgeEndo, Johnson City, TN), and R-Pilot instruments (VDW, Munich, Germany) (44 per group) were selected. Design was assessed through stereomicroscopy (blades, helical angle, measuring lines, and deformation) and scanning electron microscopy (symmetry, cross section, tip, and surface finishing). NiTi ratios were measured by energy-dispersive X-ray spectroscopy and phase transformation temperatures by differential scanning calorimetry. Microhardness and mechanical performance (torsion, bending, and buckling resistance tests) were also evaluated. Statistical analyses were performed with the Mood median test with a significance set at 5%.
Results: The Edge Glide Path had the lowest number of blades and the R-Pilot the greatest helical angle. All instruments had an almost equiatomic NiTi ratio, while showing different cross sections and tip geometries. The Edge Glide Path had a smoother surface finishing. The R-Pilot showed martensitic characteristics at room temperature, whereas mixed austenite plus R-phase was observed in the other instruments. The R-Pilot had higher results on the microhardness (436.8 hardness Vickers number), maximum torsion (0.9 Ncm), and buckling load (0.7 N) tests (P ˂ .05), whereas the Edge Glide Path had a superior angle of rotation (683.5˚) and the ProGlider was more flexible (144.1 gf) (P ˂ .05).
Conclusions: Differences in the design of the instruments and the phase transformation temperatures accounted for their mechanical behavior. The R-Pilot showed the highest torque, buckling, and microhardness, whereas the ProGlider instrument was the most flexible. (J Endod 2021;47:1917–1923.)
The development of nickel-titanium (NiTi) mechanical instruments overcame several limitations of hand files regarding the preparation of the root canal space. On the other hand, it was followed by some reports indicating a high risk of instrument separation, mostly when NiTi instruments were used to prepare curved or narrow root canals. A solution created to reduce this risk was the pre-enlargement of the canal space using small hand files, preliminary steps named scouting, apical patency, and glide path. Canal scouting refers to the initial canal negotiation with passive, small, and flexible files attempting to progress toward the apex up to the provisional working length, whereas apical patency aims to pass a small file beyond the root length, ensuring full access to the main apical foramen. After working length determination, the glide path aims to create a smooth and reproducible trajectory from the main canal orifice to the foramen. In clinical practice, this is usually achieved when a stainless steel size 10 K-file fits loosely in the canal. Together, these preliminary procedures aim to extend the life of the mechanical instruments that will be used for further canal enlargement by controlling the torsional stress over them and, consequently, decreasing the incidence of fracture or other iatrogenic mishaps.
Currently, some companies developed rotary and reciprocating NiTi instruments to perform the glide path procedure in a single step. For example, the ProGlider (Dentsply Sirona, Ballaigues, Switzerland) is a rotary instrument made of M-Wire NiTi alloy with a 0.16-mm tip diameter and a progressive taper (from 2%–8%). The Edge Glide Path (EdgeEndo, Johnson City, TN) also works with rotary motion, but it is made of a heat-treated FireWire NiTi alloy with a 0.19-mm tip size and a variable taper (https://web.edgeendo.com/ edgeglidepath/). More recently, taking the advantages of the reciprocation kinematic, the R-Pilot (VDW, Munich, Germany) was introduced to the market. This instrument is made of M-Wire NiTi alloy and has a 0.125 tip size with a constant taper of 0.047.
Up to now, only a few studies assessed the mechanical performance of the ProGlider and R-Pilot instruments, but there is scarce information on the Edge Glide Path. In fact, there is 1 article in which the mechanical properties of the latter were tested; however, at that time, the tip size of the Edge Glide Path was 0.16 mm, and, currently, it is 0.19 mm. The literature also lacks information regarding the metallurgical features and the fine microscopic design, such as surface finishing, and the mechanical behavior of glide path instruments. Therefore, the purpose of this study was to evaluate the ProGlider, Edge Glide Path, and R-Pilot instruments using a multimethod assessment to analyze their mechanical performance (torsional, bending, and buckling stress), overall design, microhardness, phase transformation temperatures, and NiTi ratio. The null hypothesis to be tested was that there were no differences regarding the mechanical performance of the ProGlider, Edge Glide Path, and R-Pilot instruments.
Material and methods
A total of 132 new ProGlider, Edge Glide Path, and R-Pilot NiTi glide path instruments (44 per group) (Table 1) were tested regarding their geometric design, metallurgical characteristics, and mechanical performance.
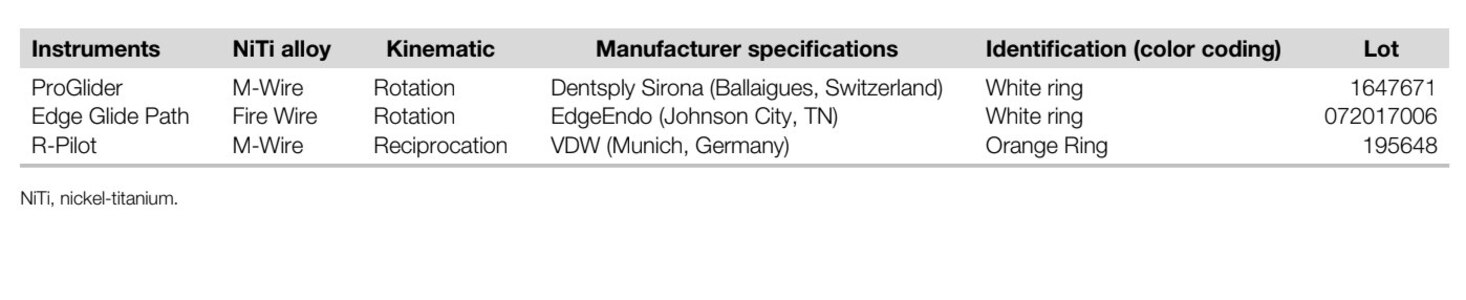
Instrument Design
Six randomly selected instruments from each system were examined under stereomicroscopy at X3.4 and X13.6 magnifications (Opmi Pico; Carl Zeiss Surgical, Germany) according to the following:
- The number of active blades (in units)
- The helical angle (average measurements of the 6 most coronal and better visible angles of the active blade assessed in triplicate)
- The distance (in millimeters) from the 2 measuring lines (20 and 22 mm) to the instruments’ tip were made in triplicate (and averaged) using a 0.01-mm resolution digital caliper (Mitutoyo, Aurora, IL); significant discrepancies in the line positions were identified when measurements were higher than 0.1 mm from the reference value
- The detection of major defects or deformations such as missed, twisted, or distorted blades
Additionally, the same instruments were evaluated regarding the spirals’ symmetry in the active part (symmetrical or asymmetrical); the tip geometry (active or nonactive); the cross-sectional shape; and the presence of surface marks, deformations, or defects produced by the machining process under conventional scanning electron microscopy (S- 2400; Hitachi, Tokyo, Japan) at X100 and X 500 magnifications.
Metallurgical Characterization
The metallurgical features of the instruments and their semiquantitative elemental constitution were analyzed with differential scanning calorimetry (DSC) (DSC 204 F1 Phoenix; Netzsch-Gerätebau GmbH, Selb, Germany) and energy-dispersive X-ray spectroscopy (Bruker Quantax, Bruker Corporation, Billerica, MA) with scanning electron microscopy (S-2400), respectively. Three instruments of each system were evaluated regarding elemental constitution with energy-dispersive X-ray spectroscopic/ scanning electron microscopic analysis (20 kV and 3.1 A) positioned at a 25-mm distance on their surfaces (400 mm2) using a dedicated software with ZAF correction (Systat Software Inc, San Jose, CA). DSC analysis was conducted according to the guidelines of the American Society for Testing and Materials (ASTM) by evaluating fragments (3–5 mm in length and 7–10 mg in weight) of the active coronal portion of 2 instruments from each system. Each fragment was exposed to a chemical bath (45% nitric acid, 30% distilled water, and 25% hydrofluoric) for 2 minutes and then mounted in an aluminum pan with an empty pan serving as the control. Thermal cycles were performed under a gaseous nitrogen (N2) atmosphere with temperatures ranging from 150˚C to -150˚C (cooling/ heating rate = 10 K/min). Transformation temperature charts were created with a dedicated software (Netzsch Proteus Thermal Analysis, Netzsch-Gerätebau GmbH). In each group, the DSC test was performed twice to confirm the results.
Mechanical Tests
The mechanical behavior of instruments was evaluated using torsional (maximum torque and angle of rotation), bending, and buckling resistance tests. Tests were performed at room temperature (approximately 21˚C) after confirming no deformation or defects on the surface of the instruments under stereomicroscopy (X13.6 magnification). The sample size was estimated for each test by taking the largest difference obtained after 6 initial measurements of 2 instruments with 80% power and an alpha-type error of 0.05. For the maximum torque (effect size = 0.47 ± 0.28, Edge Glide Path vs R-Pilot), angle of rotation (effect size = 369.7 ± 186.1, Edge Glide Path vs R-Pilot), maximum bending load (effect size = 195.9 ± 82.7, ProGlider vs Edge Glide Path), and buckling test (effect size = 0.33 ± 0.19, Edge Glide Path vs R-Pilot), a total of 7, 6, 5, and 7 instruments per group were determined, respectively. A final sample size for each test was then established as 10 instruments per group.
An international specification was used for the torsional and bending resistance tests. In the torsional test, the maximum torque (in Ncm) and the angle of rotation (in degrees) before fracture were assessed after clamping the apical 3 mm of each instrument and rotating it into a clockwise (ProGlider and Edge Glide Path) or counterclockwise (R-Pilot) direction on a constant pace (2 rotations/min) until rupture (TT100 Odeme Dental Research, Luzerna, Santa Catarina, Brazil). In the bending test, instruments were mounted in the file holder of the motor and positioned at 45˚ in relation to the floor, whereas their apical 3 mm was attached to a wire connected to a universal testing machine (EMIC DL-200 MF; EMIC, São José dos Pinhais, Brazil). The maximum load required to displace the instrument in 45˚ (using a load of 20 N and 15 mm/min of constant speed) was recorded in gram/force (gf). In the buckling test, each instrument’s handle was fixed to the head of a universal testing machine (Model 4502, series no. H3307; Instron Corp, Bucks, UK) equipped with a 1-kN load cell on a perpendicular position to the floor with the tip touching and established on a small slot in a stainless steel base. A compressive load of 1 mm/min was applied to the axial direction from the handle to the tip of the instrument until a lateral displacement of 1 mm occurred. The maximum load was recorded in newtons.
Microhardness Test
Microhardness was tested by making indentations in each instrument using a Vickers hardness tester (Duramin; Struers Inc, Cleveland, OH). The sample size was calculated by taking into consideration the largest difference obtained by performing 5 indentations in 2 different instruments (R-Pilot vs Edge Glide Path). A total of 9 indentations were required to observe a difference among groups with an effect size of 57.8, standard deviation of 39.6, power of 80%, and alpha of 0.05. However, because the calculation did not include the third group, the sample size was increased to 15 indentations (5 indentations performed in 3 instruments of each group). For this test, each instrument was prepared according to ASTM standards and stabilized using an acrylic support. A diamond penetrator was set to perform a 100-gf press load for 15 seconds. The evaluation was performed using X40 magnification, and the results were expressed as the hardness Vickers number (HVN).
Statistical Analysis
The Shapiro-Wilk test was used to check the normality of data distribution. The results from the maximum torque, angle of rotation, maximum bending load, buckling load, and microhardness were compared among groups with the nonparametric Mood median test with a significance level set at 5% (SPSS v22.0 for Windows; SPSS Inc, Chicago, IL). The results were summarized as the median and interquartile range.
Results
Instrument Design
The highest number of blades was observed in the ProGlider instrument (n = 21) followed by the R-pilot (n = 17) and the Edge Glide Path (n = 11). The helical angles of the ProGlider and Edge Glide Path instruments were similar (21.3˚ and 18.5˚, respectively) but lower than the R-Pilot (26.1˚). The Edge Glide Path was the only instrument in which the position of the measuring lines in relation to the reference was greater than 0.1 mm. No major defects were noted in any instrument (Table 2).
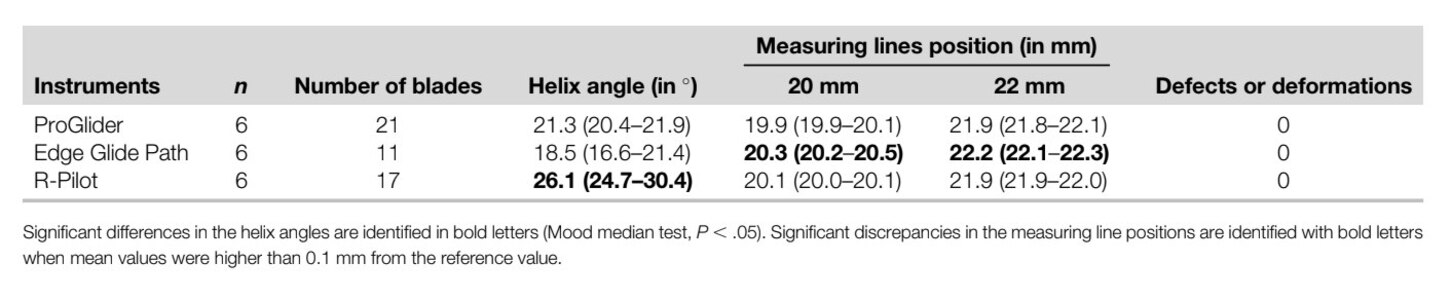
Scanning electron microscopic analysis revealed a symmetrical geometry and no radial lands in the active blade of all instruments. However, differences were observed in their cross- sectional designs (ProGlider: square; Edge Glide Path: triangular; and R-Pilot: S-shaped) and tips. The surface finishing of the ProGlider and R-Pilot had parallel horizontal marks resulting from the manufacturing process, whereas the Edge Glide Path showed a smooth surface (Fig. 1).
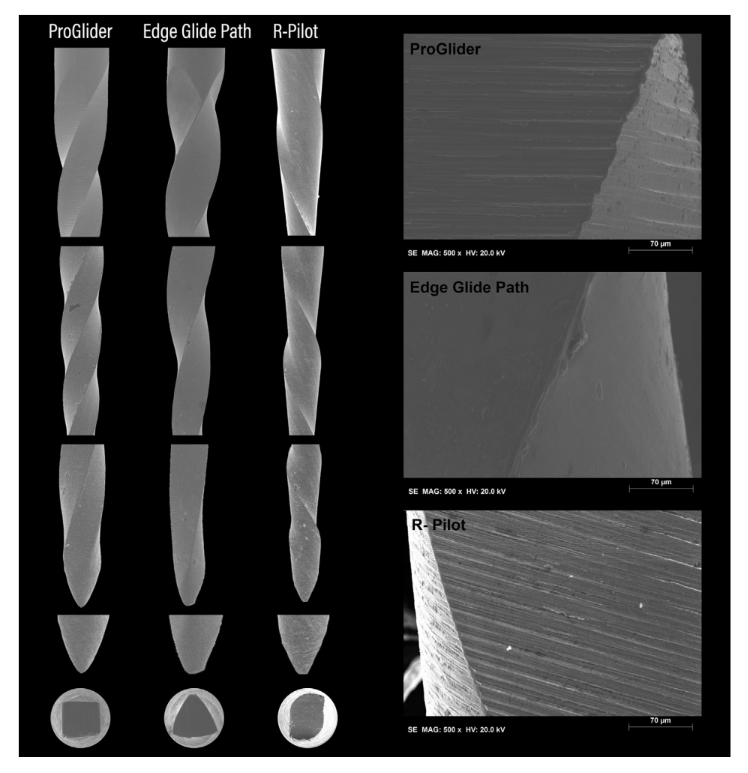
Metallurgical Characterization
Energy-dispersive X-ray spectroscopic/ scanning electron microscopic analysis showed an almost equiatomic ratio of nickel and titanium alloys in all tested instruments, without traces of other metallic elements. DSC analysis confirmed that all instruments had martensitic characteristics at room temperature (20˚C). The R-phase start temperatures at cooling were 50.3˚C (ProGlider), 33.0˚C (Edge Glide Path), and 50.4˚C (R-Pilot), respectively. The R-phase finish temperatures of the ProGlider (13.8˚C) and Edge Glide Path (16.2˚C) under 20˚C showed mixed austenite plus R-phase at room temperature, whereas the R-phase finish temperature of the R-Pilot was higher (23.3˚C) (Fig. 2).
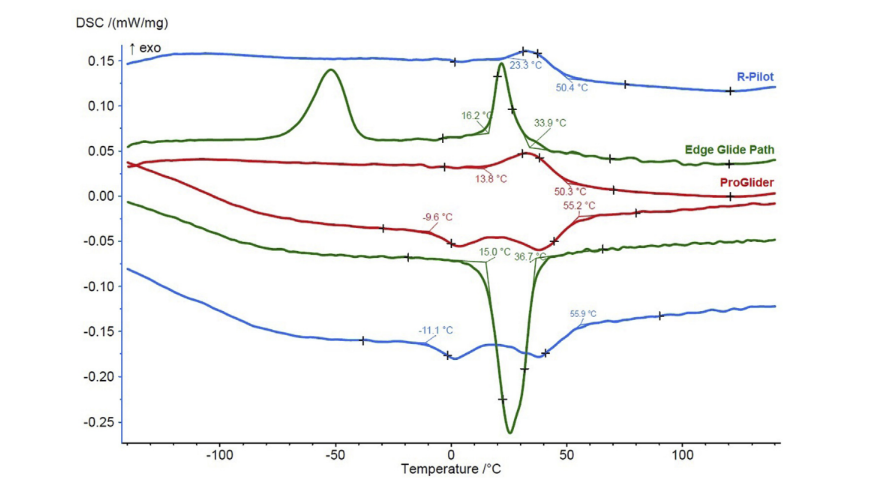
Mechanical Tests
The R-pilot instrument showed higher median values of maximum torque (0.9 Ncm) and buckling (0.7 N) than the Edge Glide Path and ProGlider instruments (P ˂ .05), which presented similar results (P ˃ .05). In the other tests (angle of rotation and bending load), statistically significant differences were observed among instruments (P ˂ .05). The Edge Glide Path showed the highest median angle of rotation (662.5˚) and maximum bending load (329.9 gf) (P ˂ .05), whereas the lowest values of the angle of rotation and bending load were observed with the R-pilot (267.5˚) and ProGlider (145.7 gf) instruments (P ˂ .05), respectively (Table 3).
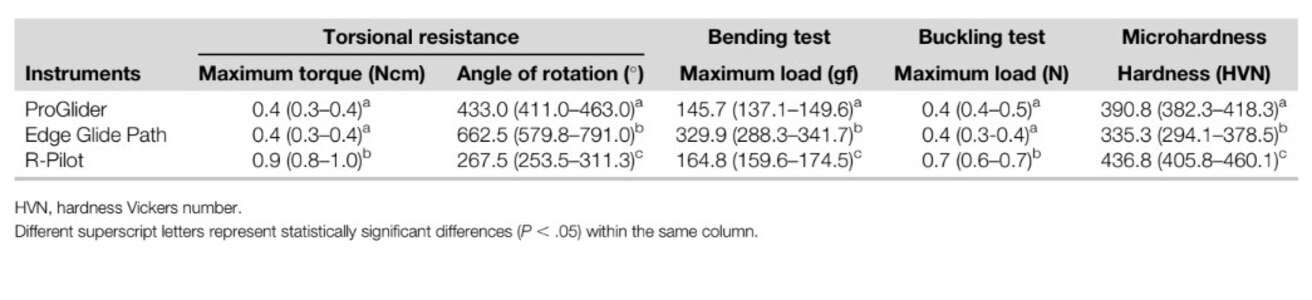
Microhardness
The highest and lowest microhardness values were noted in the R-Pilot (436.8 HVN) and Edge Glide Path (335.3 HVN) instruments, respectively (P ˂ .05) (Table 3).
Discussion
Over the years, several efforts were done for the development and better comprehension of the safety and mechanical efficiency of rotary and reciprocating NiTi systems.
However, most of the studies were designed to compare a few instruments using 1 or 2 methods. This simplified approach is usually easy to be accomplished and provides clinicians with reader-friendly information, but its major drawback is the compartmentalization of knowledge, which may result in a superficial interpretation and oversimplification of the results. In endodontics, aiming to overcome this limitation, the multimethod research has been advocated. In this approach, quantitative and qualitative analytical methods, with particular strengths to specific research levels, are performed together with the aim to explain, in a more comprehensive manner, the mechanical properties of instruments.
Although it may lead to a more complex analysis, it also increases the internal validity of the research and the reliability of the results. In the present study, a multimethod approach was used to assess the characteristics of 3 glide path NiTi instruments following international guidelines or well-established and validated methodologies. The overall geometry of the instruments was assessed using stereomicroscopy for major components and scanning electron microscopy for fine details. International guidelines were followed for DSC, microhardness, torsional and bending assays, whereas the buckling test was performed according to a previously validated methodology. Considering the lack of standardized guidelines to perform the cyclic fatigue test in NiTi instruments and the fact that lately this method was involved in several controversies in the literature, this test was not included in this study.
Torsion consists of a twisting axial force when 1 portion of the instrument rotates at a different pace of another one. The maximum torque represents the ability of an instrument to sustain that twisting axial force before rupture, whereas the angle of rotation refers to the capacity to sustain a deformation under this same force before fracture. These properties are especially useful when shaping narrow root canals, an anatomic condition that demands a high efficiency from the glide path NiTi instruments. In addition, it is important that mechanical instruments have an adequate buckling strength to allow applying light apical pressure in their long-axis direction during canal enlargement. A high flexibility, which is evaluated by the bending test, is also required to avoid deviation of the original canal pathway while performing the glide path procedure. In the present study, results from the mechanical tests (maximum torque, angle of rotation, bending load, and buckling strength) revealed differences among instruments, and the null hypothesis was rejected. It is important to point out that differences observed in the overall design (Table 2), surface finishing (Fig. 1), and phase transformation temperatures (Fig. 2) highly influenced the mechanical performance of the tested instruments (Table 3).
The highest torque resistance and the lowest angle of rotation values were observed with the R-Pilot instrument (Table 3). Although the R-pilot had the smallest tip size among the tested instruments, its large diameter at D3, a position in which the file is locked and rotated during the torsional test, tend to sustain a higher torque and lower angular rotation, which may explain these results. On the other hand, the ProGlider and Edge Glide Path instruments showed similar torque resistance values but different angles of rotation. The former can be partially explained by their similar metal constitution with mixed austenite plus R-phase (Fig. 2), whereas the latter is possible due to the smoother finishing surface of the Edge Glide Path (Fig. 1), which tends to make the instrument less prone to crack propagation during torsion.
In the bending resistance test, the number of spirals per millimeter, along with potential differences in the heat treatment of their metal alloys, seemed to have influenced the results more than the remaining evaluated parameter. For instance, the most and the least flexible instruments, the ProGlider and the Edge Glide Path, also had the highest and lowest number of spirals (Table 2), respectively, whereas the R-Pilot had intermediate values. According to McSppaden, in similar conditions, the more spirals in the active blade of an NiTi instrument, the greater the helical angle and flexibility, which could explain these results. In the buckling test, differences in the alloy crystallographic arrangement and dimensions of the instruments had a relevant impact on the results. During the buckling test, lateral displacement under a compressive load appears mostly at the apical region of the instruments. Therefore, the higher buckling strength of the R-Pilot (Table 3) might be related to its larger diameter at 4–5 mm from its tip compared with the other instruments.
Interestingly, instruments with low (Edge Glide Path: 335.3 HVN), intermediate (ProGlider: 390.8 HVN), and high (R-Pilot: 436.8 HVN) microhardness values showed similar raking in the buckling test, suggesting that buckling results were affected by the particular crystal arrangements in the nickel and titanium elements of each instrument, which partially explains the results.
Overall, the high maximum torque and buckling resistance of the R-Pilot as well as the high flexibility of the ProGlider corroborate previous findings. Although the microhardness of the ProGlider and R-Pilot M-Wire alloy was not addressed yet, the results match somewhat with values reported for the NiTi alloy of other instruments. Unfortunately, a comparison of the Edge Glide Path results with previous publications was not possible considering that, so far, none of them evaluated the new generation of this instrument with a tip size of 0.19 mm (https:// web.edgeendo.com/edgeglidepath/), instead of 0.16 mm.
Regarding the clinical significance of the mechanical outcomes, it is of note that the tested glide path instruments were different from each other in all aspects. It helps to explain the superior strength and flexibility of the R-Pilot (high torque and buckling associated to a low bending load), whereas the Edge Glide Path showed the opposite.
The glide path procedure has been proven to be very effective to control the fracture rate of mechanical NiTi instruments used for root canal preparation. However, this preliminary procedure demands high technical skills even for experienced clinicians. This is the main reason why instruments developed for mechanical glide path are so important in clinical practice. In the present study, the R-Pilot instrument showed superior strength and flexibility (high torque and buckling associated to a low bending load), whereas the Edge Glide Path showed the opposite. At first sight, these results could be interpreted as an indication that in a clinical setup the R-Pilot, among the tested instruments, would be the most effective for the glide path procedure in calcified and/or curved canals. Unfortunately, translating science from the laboratory to the clinic is not a straightforward process because systematic basic research is directed toward a better knowledge or understanding of the fundamental aspects of observable facts. In the health field, although extensive resources have been dedicated to both laboratory and clinical research throughout the years, significant barriers existed between them. In fact, in endodontics, translational research—a discipline that takes scientific discoveries made in the laboratory in the clinic or out in the field and transforms them into new approaches to improve health care—is still a discipline to be explored.
Although the use of a specific temperature in tests such as cyclic fatigue is not consensual or standardized, in the mechanical tests conducted in the present research, this variable has not been previously explored and a lack of information still exists. One study addressed the torsional test under 2 different temperatures and found no difference on the tested instruments. The present tests were conducted at room temperature within the range recommended by ASTM E92-17 international standards. The strength of the present study was to compare the mechanical efficiency of 3 different glide path instruments using a multimethod assessment and explain the results on the basis of their design, phase transformation temperature, microhardness, and overall geometry. On the other hand, a limitation of this study is the lack of information regarding the dimensions of the Edge Glide Path, considering that the manufacturer only provides its tip size (0.19 mm) and maximum diameter (1.0 mm). These data are often necessary to explain some results obtained in the mechanical tests. Additionally, other parameters including cutting and shaping abilities were not evaluated herein. Therefore, further studies must explore the combination of other tests using the multimethod approach to compare the efficiency and safety of glide path instruments available on the market.
Conclusions
Although tested instruments had nickel and titanium elements presented in roughly equal atomic percentages, differences observed in their overall design, surface finishing, and phase transformation temperatures were reflected in their mechanical performance. The R-Pilot showed the highest values in the torque resistance, buckling load, and microhardness tests, whereas the Edge Glide Path had a superior angle of rotation and the ProGlider the highest flexibility.
Authors: Jorge N. R. Martins, Emmanuel João Nogueira Leal Silva, Duarte Marques, Mario Rito Pereira, Sofia Arantes-Oliveira, Rui F. Martins, Francisco Manuel Braz Fernandes and Marco Aurelio Versiani
References:
- McGuigan MB, Louca C, Duncan HF. Endodontic instrument fracture: causes and prevention. Br Dent J 2013;214:341–8.
- Hülsmann M, Peters OA, Dummer PM. Mechanical preparation of root canals: shaping goals, techniques and means. Endod Topics 2005;10:30–76.
- Plotino G, Nagendrababu V, Bukiet F, et al. Influence of negotiation, glide path, and preflaring procedures on root canal shaping – terminolgy, basic concepts, and a systematic review. J Endod 2020;46:707–29.
- West JD. The endodontic glidepath: "secret to rotary safety". Dent Today 2010;29:86–93.
- Berutti E, Negro AR, Lendini M, Pasqualini D. Influence of manual preflaring and torque on the failure rate of ProTaper rotary instruments. J Endod 2004;30:228–30.
- Pasqualini D, Bianchi CC, Paolino DS, et al. Computed micro-tomographic evaluation of glide path with nickel-titanium rotary PathFile in maxillary first molars curved canals. J Endod 2012;38:389–93.
- Lopes WS, Vieira VT, Silva E, et al. Bending, buckling and torsional resistance of rotary and reciprocating glide path instruments. Int Endod J 2020;53:1689–95.
- Keskin C, Inan U, Demiral M, Kelesx A. Cyclic fatigue resistance of R-Pilot, WaveOne Gold Glider, and ProGlider glide path instruments. Clin Oral Investig 2018;22:3007–12.
- Lee JY, Kwak SW, Ha JH, et al. Mechanical properties of various glide path preparation nickel- titanium rotary instruments. J Endod 2019;45:199–204.
- Anderson ME, Price JW, Parashos P. Fracture resistance of electropolished rotary nickel-titanium endodontic instruments. J Endod 2007;33:1212–6.
- de Vasconcelos RA, Murphy S, Carvalho CA, et al. Evidence for reduced fatigue resistance of contemporary rotary instruments exposed to body temperature. J Endod 2016;42:782–7.
- Hieawy A, Haapasalo M, Zhou H, et al. Phase transformation behavior and resistance to bending and cyclic fatigue of ProTaper Gold and ProTaper Universal instruments. J Endod 2015;41: 1134–8.
- Martins JN, Silva E, Marques D, et al. Mechanical performance and metallurgical features of ProTaper Universal and 6 replicalike systems. J Endod 2020;46:1884–93.
- ASTM International. ASTM F2004 2 17: standard test method for transformation temperature of nickel-titanium alloys by thermal analysis. West Conshohocken, PA: ASTM International; 2004. p. 1–5.
- ISO 3630-3631:2008. Dentistry – root canal instruments – part 1: general requirements and test methods. Geneva, Switzerland: ISO; 2008.
- Lopes HP, Elias CN, Mangelli M, et al. Buckling resistance of pathfinding endodontic instruments. J Endod 2012;38:402–4.
- ASTM International. ASTM E92-17: sStandard test methods for Vickers hardness and Knoop hardness of metallic materials. West Conshohocken, PA: ASTM International; 2017. p. 1–27.
- De-Deus G, Silva EJ, Vieira VT, et al. Blue thermomechanical treatment optimizes fatigue resistance and flexibility of the Reciproc files. J Endod 2017;43:462–6.
- Hülsmann M, Donnermeyer D, Sch€afer E. A critical appraisal of studies on cyclic fatigue resistance of engine-driven endodontic instruments. Int Endod J 2019;52:1427–45.
- Gambarini G. Cyclic fatigue of ProFile rotary instruments after prolonged clinical use. Int Endod J 2001;34:386–9.
- Kramkowski TR, Bahcall J. An in vitro comparison of torsional stress and cyclic fatigue resistance of ProFile GT and ProFile GT Series X rotary nickel-titanium files. J Endod 2009;35:404–7.
- Schoenfeld A. On having and using geometric knowledge. In: Hiebert J, editor. Conceptual and Procedural Knowledge: The Case of Mathematics. 1st ed. Hillsdale, NJ: Lawrence Erlbaum Associates; 1986.
- Mandl H, Gruber H, Renkl A. Chapter 8 Misconceptions and knowledge compartmentalization. Adv Psychol 1993;101:161–76.
- Silva E, Martins JN, Lima CO, et al. Mechanical tests, metallurgical characterization and shaping ability of Niti rotary instruments: a multimethod research. J Endod 2020;46:1485–94.
- Creswell JW. Research Design: Qualitative, Quantitative and Mixed Methods Approaches. 4th ed. Thousand Oaks, CA: Sage Publications; 2014.
- Hülsmann M. Research that matters: studies on fatigue of rotary and reciprocating NiTi root canal instruments. Int Endod J 2019;52:1401–2.
- McSpadden JT. Mastering the concepts. In: McSpadden JT, editor. Mastering Endodontics Instrumentation. Chattanooga, TN: Cloudland Institute; 2007. p. 7–36.
- Cheung GS, Darvell BW. Fatigue testing of a NiTi rotary instrument. Part 2: fractographic analysis. Int Endod J 2007;40:619–25.
- McSpadden JT. Mastering instrument designs. In: McSpadden JT, editor. Mastering Endodontics Instrumentation. Chattanooga, TN: Cloudland Institute; 2007. p. 37–97.
- Yilmaz OS, Keskin C, Aydemir H. Comparison of the torsional resistance of 4 different glide path instruments. J Endod 2021;47:970–5.
- Woolf SH. What is translational science. JAMA 2008;299:211–3.
- Martins JN, Silva EJ, Marques D, et al. Design, metallurgical features, mechanical performance and canal preparation of six reciprocating instruments. Int Endod J 2021;54:1623–37.
- Silva EJ, Giralds JF, Lima CO, et al. Influence of heat treatment on torsional resistance and surface roughness of nickel-titanium instruments. Int Endod J 2019;52:1645–51.